Packinox
A Packinox heat exchanger is ideal for demanding heat recovery duties in processes with high pressures and temperatures. Its outstanding thermal performance, superior hydraulic efficiency and low CAPEX allow you to optimize energy efficiency, increase profitability and improve sustainability. A Packinox enables higher yield and recovers more heat than a shell-and-tube solution, resulting in better ROI and a lower environmental impact. Packinox is also available as plate-and-frame configuration.
Reliable efficiency
- Lower OPEX – The high heat recovery leads to substantial energy savings. Maintenance costs are also low thanks to minimal fouling.
- Lower CAPEX – A single Packinox can replace several large shell-and-tubes and makes it possible to operate processes with smaller furnaces and cooling
- Higher process yield thanks to a low pressure drop, optimal liquid/gas mixing, high operating flexibility and a fully customized design.
- Reliable, proven technology – More than 350 units in operation worldwide.
- Real-time monitoring and continuous optimization by Alfa Laval experts.
Packinox+
Thanks to our new FlexFlow technology, a Packinox+ heat exchanger can be optimized for highly asymmetric flows and offers a range of flow configurations, including multi-stream arrangements, making it highly suitable for a broad spectrum of demanding process duties.
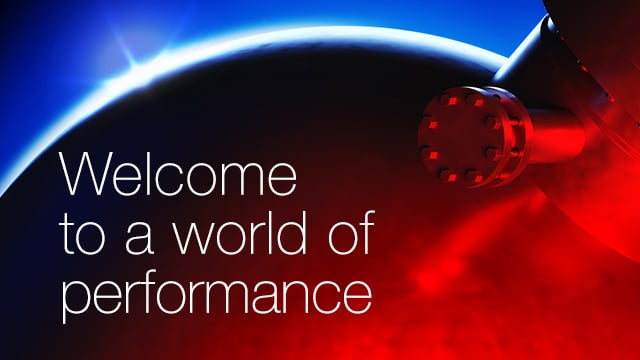
Sustainable solutions
Imagine a more sustainable world. A world where it takes less to produce even more. A world where we efficiently meet our growing energy demands and simultaneously reduce CO2 emissions. Imagine a world where we can harness the power of natural resources, while preserving them at the same time. At Alfa Laval, we don’t just imagine this world. We’re building it – together with our customers and our partners.
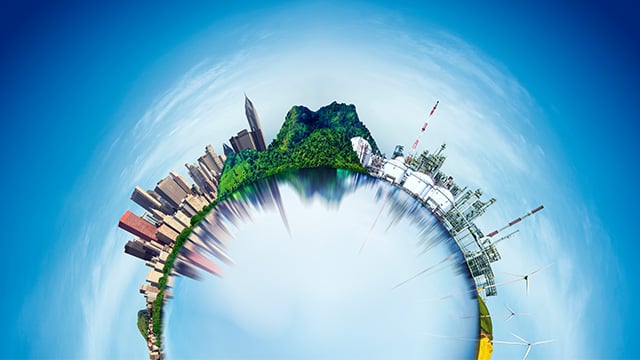
Packinox plate-and-frame heat exchanger
The plate-and-frame version of Alfa Laval Packinox has no pressure shell and no Spray Bar system. It is suitable for applications where the extra pressure and temperature resistance provided by the shell is not required, and where no separate liquid feed injection/flash evaporation takes place inside the heat exchanger. Applications include carbon capture and storage, energy storage, oil refining, petrochemicals and many more.
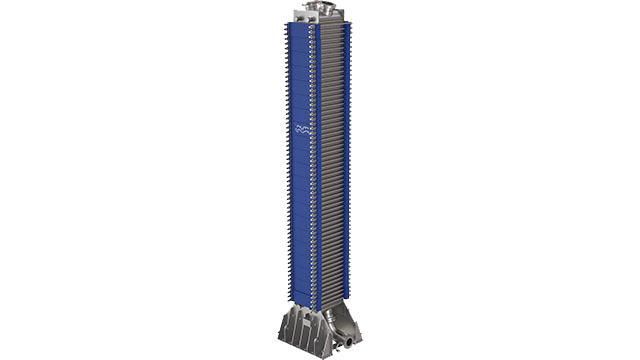
Rethink your refinery
We support all stages of your project - from initial idea generation, through the feasibility- and basic design study, to installation and commissioning of our equipment. Working closely with licensors, engineering companies and end-users, Alfa Laval’s refinery team brings world-leading expertise in process optimization to all types of refinery projects, maximizing the probability of project success and ROI.
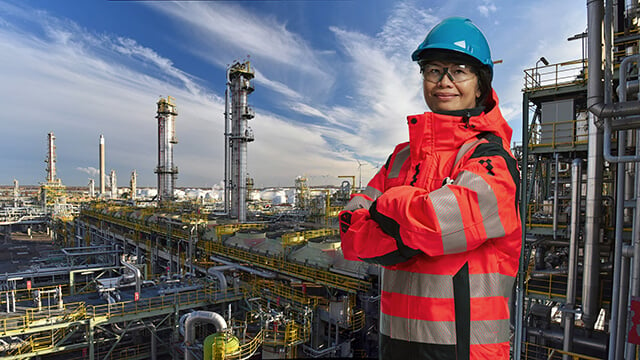
Unique HyperCut plate design improves thermal efficiency
Alfa Laval’s unique HyperCut heat transfer plates have many benefits:
- 50% lower pressure drop over the distribution areas compared to the previous design. This makes it possible to either increase heat recovery, reduce the size of the heat exchanger or to lower the overall pressure in the process.
- 30% higher mechanical strength and higher resistance to thermo-mechanical stress.
- Improved flow and pressure distribution, which improves operability.
Kako radi
The recycle gas enters the heat exchanger at the bottom and passes the Spray Bars on its way into the plate pack. The liquid feed enters from the side and is sprayed into the gas by the Spray Bars. This ensures a perfect mix of liquid feed and recycle gas, which facilitates lifting and makes it possible to operate the unit on a high liquid-to-gas ratio for maximum yield.
The feed/gas mixture moves up through the plate pack while the reactor effluent travels in the opposite direction. The highly turbulent, counter-current flow ensures that most of the heat from the reactor effluent is recovered and heats the cold feed. The hot approach temperature can be as low as 25°C (45°F).
The outstanding heat recovery reduces the load on both the reactor heater and the cooling system compared to using other types of heat exchangers, thereby reducing both OPEX and CAPEX.
Customer stories
Learn how companies around the world, in various industries, have ensured maximum flexibility, reliability and yield with Alfa Laval Packinox heat exchangers.
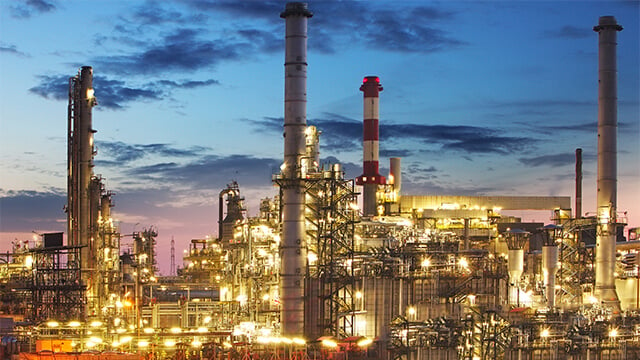
Unique features
Plate Wash
Monitors the pressure drop in the heat exchanger and allows operators to engage water cleaning whenever ammonium salt fouling begins to accumulate.
Get the latest news on LinkedIn
Stay tuned to our LinkedIn page for the latest news on Alfa Laval Packinox heat exchangers.
